I know this is a long shot, but I am looking anywhere I can for this data. I'll probably be emailing a few different HQ partners, but want to make sure I've done my due diligence looking myself first.
When a TM pulls a batch like a One for One or Out-of-Stock, and they tell the myDevice that the item being requested at a given location is not there, this is an INF (Item not found). The system catalogues a backroom error, i.e. a ghost, and the item is deleted from the backroom location. This activity is well recorded in Greenfield datasets like Assets_Protection_EDABI.AP_BACKROOM_DPCI_PULL_BKSTK, StoreLogistics.MOVE_BRLA_FROM_BIGRED_MYDAYMYWORK, and surely others. With the right card and filters, its generally relatively easy to identify the source of the error.
By contrast, when a fulfillment TM picks a batch with items that have backroom locations, I can't find anything that record instances of them INF'ing the backroom location. But surely that is happening, right? The FF team, on the whole, interacts more with backroom than any other team. Over time, you'd expect them to encounter instances where the items weren't backstocked correctly or other times where the TM just didn't look hard enough. In my mind, it should create a ghost just like when a puller says item not found. Yet BRLA metrics are not impacted by FF TMs.
Now, I have really looked hard for this and recently found the following dataset: FlexFulfillment.BATCHING_METRICS_PICK_ITEM_DETAIL, which looks extremely promising when examining its dimensions and metrics. I spent time formatting a card to utilize it:
I thought great, I've got it! But as I began researching each INF activity, what I realized was that it wasn't showing INF from the backroom. Instead what it's showing are instances where an item was INFd after first having some of the quantity fulfilled from the backroom. Useless!
What I want to see is any time the picked BR quantity differed from the expected BR quantity. If anyone has thoughts on this, I would be extremely grateful.
When a TM pulls a batch like a One for One or Out-of-Stock, and they tell the myDevice that the item being requested at a given location is not there, this is an INF (Item not found). The system catalogues a backroom error, i.e. a ghost, and the item is deleted from the backroom location. This activity is well recorded in Greenfield datasets like Assets_Protection_EDABI.AP_BACKROOM_DPCI_PULL_BKSTK, StoreLogistics.MOVE_BRLA_FROM_BIGRED_MYDAYMYWORK, and surely others. With the right card and filters, its generally relatively easy to identify the source of the error.
By contrast, when a fulfillment TM picks a batch with items that have backroom locations, I can't find anything that record instances of them INF'ing the backroom location. But surely that is happening, right? The FF team, on the whole, interacts more with backroom than any other team. Over time, you'd expect them to encounter instances where the items weren't backstocked correctly or other times where the TM just didn't look hard enough. In my mind, it should create a ghost just like when a puller says item not found. Yet BRLA metrics are not impacted by FF TMs.
Now, I have really looked hard for this and recently found the following dataset: FlexFulfillment.BATCHING_METRICS_PICK_ITEM_DETAIL, which looks extremely promising when examining its dimensions and metrics. I spent time formatting a card to utilize it:
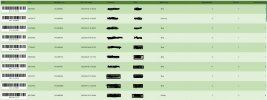
I thought great, I've got it! But as I began researching each INF activity, what I realized was that it wasn't showing INF from the backroom. Instead what it's showing are instances where an item was INFd after first having some of the quantity fulfilled from the backroom. Useless!
What I want to see is any time the picked BR quantity differed from the expected BR quantity. If anyone has thoughts on this, I would be extremely grateful.
Last edited: